Research of A.K.M. Nazrul Islam
Research Interests
The core research interests include the following:
- Hydrogen Gas Turbine
- Combustion
- Lifted Flame
- Energy
- Energy-efficient Data Center Design
Currently, he is actively engaged in research on Premixed hydrogen combustion systems for gas turbines.
Premixed hydrogen combustion system for gas turbine
Partial-premixed hydrogen combustion systems for gas turbines offer a promising path toward cleaner and more efficient power generation. By thoroughly mixing hydrogen and air before ignition, these systems achieve significantly lower nitrogen oxide (NOx) emissions than traditional combustion methods. This technology is crucial for the increasing adoption of hydrogen as a fuel, as it addresses the challenges associated with hydrogen’s high flammability and wide explosion limits. However, developing robust and stable premixed combustion systems requires careful consideration of factors such as fuel-air ratio, ignition timing, and combustor geometry to prevent flashback and ensure optimal performance.
One article was presented at the ASME Turbomachinery Technical Conference & Exposition (Turbo Expo) 2025. Title of the article: Investigation of Combustion Characteristics of Hydrogen Lifted Flame in A Small Hydrogen Combustion Chamber.
The 53rd Annual Conference of the Gas Turbine Society of Japan has accepted another abstract. Title of the abstract: Flow Field Visualization of Hydrogen-Lifted Flame in a Combustion Chamber Using the Schlieren Imaging Method.

Utilization of exhaust heat from diesel engine by Organic Rankine Cycle (ORC)
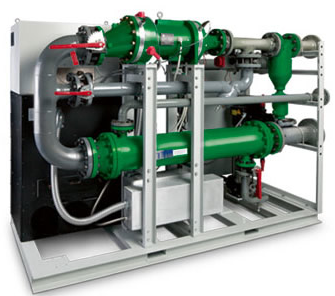
Research has been conducted to improve diesel engine performance using the Organic Rankine Cycle (ORC), which utilizes exhaust gas and jacket water cooling systems.
A journal article is under preparation. Title of the abstract “Performance Improvement of Diesel Engine by Organic Rankine Cycle (ORC) Utilizing Heat From Exhaust Gas and Jacket Water Cooling System”.
Sophisticated technology for gas turbine blade cooling systems
Special cooling technologies are essential to cool gas turbine airfoils to maximize thermal efficiency. Internal cooling technology is widely used in modern gas turbine airfoils for high cooling performance. Among different internal cooling techniques, a teardrop-shaped dimple surface is a prominent method for high heat transfer performance and low–pressure drop.
I performed research by transient technique to investigate the effects of rotation-angle of teardrop-shaped dimples on heat transfer enhancement with compensation of three-dimensional heat conduction analysis. The experimental results revealed that the highest heat transfer occurred at 30 deg rotated dimpled surface at the Reynolds number of 16,000 to 36,000. The highest friction factor was found at 30 deg dimpled surface and the lowest friction factor was found at 0 deg dimpled surface. The overall heat transfer performance of the airfoil internal cooling was evaluated in terms of heat transfer efficiency index and the maximum value was found for 30 deg rotated dimpled surface.
One article was published by the International Heat Transfer Conference (IHTC-16) held in Beijing, China during August 10~15, 2018. Title of the article: Effects of Rotation Angle of Teardrop-Shaped Dimples on Heat Transfer Enhancement of Airfoil Internal Cooling Investigated by Transient Technique
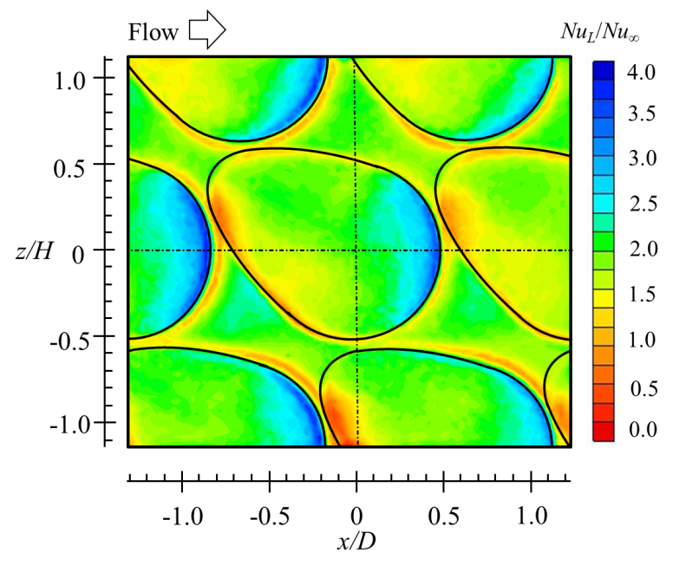
Heat Transfer Study on a Solid with Protective Fabric Under Hot Air Jet Impingement
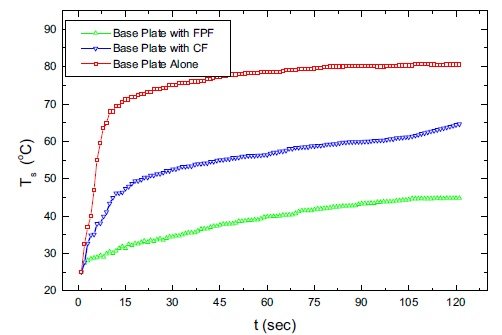
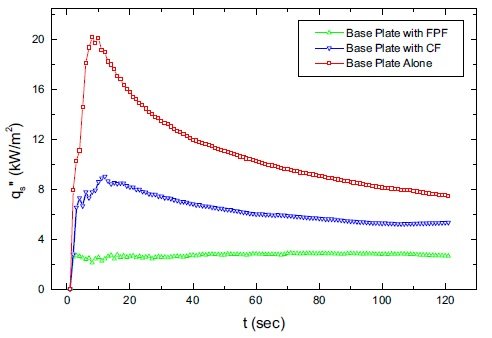
This research project investigated the thermal response of a solid base plate (mimicking the skin) and fire-protective fabric’s performance under hot air jet impingement situations. This investigation utilized a fabricated attachment with an axial flow wind tunnel for a horizontal hot air jet of different velocities and temperatures impinged on a vertical base plate. The experiments were conducted without fabric, cotton fabric, and fire-protective fabric to understand the unprotected and protective conditions. The air jet temperatures were 115 C and 125 C. The hot air jet velocities were 12, 15, and 19 m/s at the exit point of the nozzle. The variations of the nozzle-to-plate separation were 2, 4, and 6 for nozzle diameter. The fabrics were placed in contact and 6 mm away from the base plate during the experiments. The experimental results show the maximum decrease of heat flux by using the protective fabric. Significant heat transfer also occurred for cotton fabric. In addition, heat transfer through the fabric was observed for various nozzle-to-plate separations and Nusselt numbers.
Two articles were published from this research project.
(1) Study of Transient Heat Transfer of A Solid with Protective Fabric under Hot Air Jet Impingement, published by the International Conference on Mechanical Engineering (ICME-2011), held in Dhaka, Bangladesh on December 18~20, 2018.
(2) Experimental investigation of transient heat transfer on a solid surface, with fire retardant fabric under hot air impinging jet published by Procedia Engineering, 2015, Volume 105, pp. 167-175.